PLANEJAMENTO E CONTROLE DA MANUTENÇÃO (PCM)
1. Introdução
O Planejamento e Controle da Manutenção (PCM) é uma peça importantíssima dentro da Gestão de Ativos Industriais e este artigo irá abordar alguns itens necessários para uma boa performance do PCM.
2. Explicando o PCM
Para que seja possível iniciar qualquer tipo de explanação do assunto, precisamos entender de forma simples o que é o PCM, além das palavras que simplificamos na sigla.
É costume dizer que o PCM é o coração da indústria, fundamental para que todo o processo de operação seja confiável e íntegro para que a produção de qualquer produto (energia, minério, lubrificante, óleo combustível, papel & celulose etc.) não seja interrompida. É muito além da manutenção, é a garantia que os equipamentos operem conforme projetados e de acordo com as suas especificações técnicas e características.
Entendemos, o PCM não é um setor ou “filho” da manutenção e sim da unidade operacional, ou seja, ele é o suporte de toda planta industrial, atendendo exclusivamente aquilo que é importante para a garantia da confiabilidade e integridade dos equipamentos e processos de operação, utilizando a manutenção como “ferramenta” para atender as necessidades da planta. Estruturamos o fluxograma da figura 1, de forma totalmente ilustrativa, sendo possível verificarmos os setores dentro de uma indústria. Podemos perceber que o PCM, assim como o SSMA é ligado diretamente a diretoria ou a Gerência da Planta, isso vai depender muito da robustez da planta industrial. Confira na figura abaixo o fluxograma ilustrativo de uma planta industrial.
O PCM recebe demandas de todos os setores, planejando, organizando e controlando os pedidos, programando as intervenções de acordo com a necessidade operacional, através de variáveis do processo como: Matriz de Criticidade, Paradas Não Programadas, Paradas Programadas, Aumento de Produtividade do Processo etc.
Destacamos a figura abaixo para ilustrar a chegada da demanda para o setor de PCM
A equipe de PCM é composta não somente de planejadores e/ou programadores de manutenção, mas também de uma equipe de Engenharia de Confiabilidade e Integridade dos ativos, que estará ligado diretamente na visão estratégica para alcance máximo da disponibilidade e gestão dos ativos.
3. Diretrizes do PCM
ERP quer dizer planejamento de recursos empresariais, mas o que o ERP significa? Para uma definição simples, pense em todos os processos industriais necessários para administrar uma Unidade Operacional: Manutenção, Inspeção, Paradas, Planejamento, Controle etc. Em seu nível mais básico, o ERP ajuda a gerenciar eficientemente todos esses processos em um sistema integrado. Ele costuma ser chamado de sistema de registro da organização.
No entanto, os sistemas ERP atuais são tudo, menos básicos, e têm pouca semelhança com o ERP de décadas atrás. Eles são agora disponibilizados na nuvem e usam as tecnologias mais recentes – como IA e Machine Learning – para fornecer automação inteligente, maior eficiência e insights instantâneos em toda a empresa. Softwares modernos de Cloud ERP também conectam operações internas a parceiros de negócios e redes em todo o mundo, proporcionando às empresas a colaboração, agilidade e velocidade imprescindíveis para serem competitivas hoje, garantindo a confiabilidade e integridade de seus ativos. Um sistema de gestão para a manutenção, é fundamental e necessário, conforme ilustrado abaixo.
Aumento da produtividade: otimizar e automatizar seus principais processos de planejamento e controle da manutenção, ajudando todos os profissionais a fazerem mais, com menos recursos, além de guiar as diretrizes nas tomadas de decisões de parada e/ou não de um equipamento, ou até mesmo em uma definição de prioridade de intervenção por parte da equipe de manutenção.
Insights de grande alcance: elimine silos de informações, criando uma fonte única da verdade e tendo respostas rápidas para questões essenciais do setor de manutenção, confiabilidade e integridade dos ativos.
Agilidade na emissão de relatórios: gere relatórios, intervenções e controle dos ativos, compartilhando os resultados com facilidade. Assim a equipe de PCM trabalhará com base em insights, melhorando o desempenho em tempo real.
Riscos menores: maximize a visibilidade e o controle dos ativos, garantindo as exigências regulatórias, prevendo e prevenindo qualquer risco inerente aos ativos.
TI mais simples: É possível utilizar aplicativos integrados de ERP que compartilham um mesmo banco de dados para simplificar as operações de TI e proporcionar um modo mais fácil de trabalhar.
Maior agilidade: identifique novas oportunidades e responda rapidamente a elas com operações eficientes e acesso direto a dados em tempo real.
3.2 O Fluxo Macro do PCM
Como todo processo, o Planejamento e Controle da Manutenção (PCM), também consiste em ter um fluxo para que toda solicitação e/ou necessidade de intervenção, seja planejada e programada de acordo com a criticidade operacional e de processos.
Assim, na figura abaixo elaboramos um fluxograma macro para facilitar o entendimento, simplificando os processos dentro da célula PCM.
3.3 Solicitação de Serviço ou Nota de Manutenção
- TAG do equipamento
- Local da anomalia
- Fotos
- Descrição e/ou texto do motivo da abertura de nota
- Especialidade a ser utilizada para resolver o problema
3.4 TAG de Equipamento
Todos os ativos da empresa têm uma identidade, que denominamos “TAG” que vem da palavra Tagueamento. É extremamente importante e fundamental que todos os equipamentos sejam cadastrados através de seu número, assumindo assim um papel fundamental na gestão do ativo, haja vista que, a partir dele, é feito o rastreamento e cadastramento das intervenções realizadas, bem como sua folha de dados, parâmetros técnicos, relatórios etc.
Existem várias formas para padronização de tagueamento dos ativos da empresa, podendo-se definir no momento de estruturação do ERP e/ou Software de Gestão dos Ativos.
É importante reforçarmos que existiu a Norma ABNT NBR 8190 que tratava o assunto de identificação industrial de tagueamento, mas que foi extinta em 02/12/2010, mas que ainda serve como parâmetro para que as empresas consigam cadastrar seus equipamentos de forma simples, objetiva e clara.
Abaixo, colocamos como exemplo um modelo de tagueamento para apoio em um cadastro de equipamentos, quando necessário.
Onde:
XXXX – Representa o Código da Empresa;
YYYY – Representa uma Área Industrial dentro da empresa;
ZZZ – Representa um Sistema dentro da Empresa;
AA – Representa uma subdivisão do sistema;
CC – Representa mais uma subdivisão;
DD – Representa mais uma subdivisão;
Na figura abaixo é possível identificar essa estrutura em um modelo exemplificativo.
3.5 Ciclo de Vida da Ordem de Manutenção
Após a abertura da Solicitação de Serviço (SS) ou Nota de Manutenção, a equipe de Planejadores faz a triagem dos serviços, conferindo as informações inseridas, gerando a Ordem de Manutenção (OM) e direcionando ao grupo de planejamento correto, para sequência do processo de execução.
Sem a existência da Ordem de Manutenção (OM) não seria possível planejar e controlar as necessidades dos processos e setores envolvidos. Nesta OM contemplará todas as informações necessárias para que o setor de planejamento identifique a anomalia, defeito e/ou falha.
3.6 Planejamento
É neste item que é dimensionado todo o recurso necessário para que seja possível resolver o problema descrito na Ordem de Manutenção (OM). Sem dúvidas é a etapa mais importante do processo, pois garante que a equipe de execução não terá problemas no momento da intervenção. Também é a responsável por garantir a segurança das pessoas e processos, levantando todos os riscos inerentes das atividades, mitigando-os com ações que garantam a máxima eficiência da segurança. O planejamento consiste em algumas etapas básicas que com elas é possível estruturar e realizar de forma completa uma intervenção, mas claro, reforço que toda indústria tem sua particularidade e que isso pode ser modificado (adicionando itens), na figura 6 demonstro um exemplo de fluxograma do planejamento.
3.6.1. Delineamento
O delineamento é o processo inicial e que determinará todos os recursos a serem utilizados na etapa de execução, seja quantidade de mão de obra, material, equipamentos, dispositivos e ferramentas. Neste item são divididos em algumas etapas:
3.6.1.1 Consultar Documentos
Antes de realizar a visita técnica em campo, o planejador deverá consultar documentos, acessando o ERP e a rede da empresa, coletando todas as informações do equipamento e local de instalação, como:
- Folha de dados de um equipamento (ilustração abaixo)
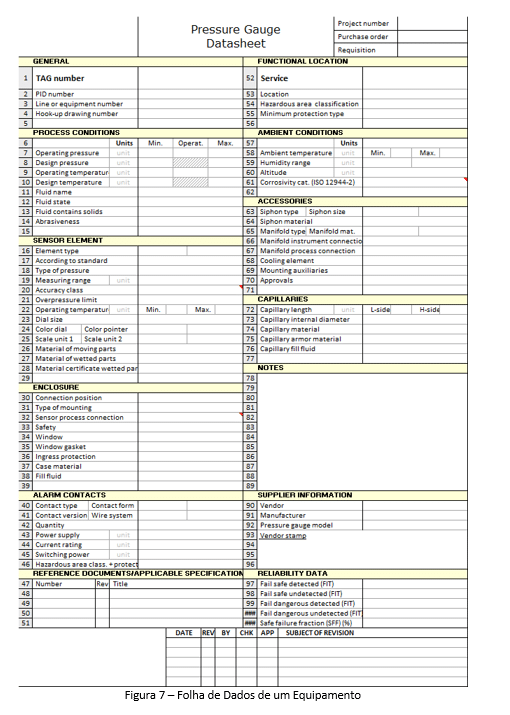
- Fluxograma de Processos
Os fluxogramas são essenciais para um bom planejamento, nele podemos identificar todo o processo de um equipamento, verificando entrada e saída dos fluídos, pressão, TAG, além de entender toda a operação de uma unidade ou local de instalação
- Lista Técnica
A lista técnica dos equipamentos é fundamental para a verificação dos materiais necessários para a intervenção dos executantes, ou seja, nela você identifica o material necessário, conforme projeto e especificação técnica, verificando seu part number (PN) que é um código padronizado para identificar componentes de um equipamento, podendo cadastrá-lo no ERP, com o código correto, mantendo atualizado, para que facilite a consulta e utilização, além de poder parametrizar este material no estoque.
Confira abaixo a imagem que lustra a lista técnica de equipamentos.
Confira abaixo a lista técnica de equipamentos através da folha de dados.
Confira abaixo a lista técnica de equipamentos cadastrada na ERP.
- Isométrico
Consultar o isométrico é fundamental para as atividades de caldeiraria e substituição de tubulações, válvulas, conexões etc.
Nele, você pode identificar as cotas de um trecho ao outro, além da lista completa de material com as suas especificações técnicas, bem como os dados de projeto e operação, como: temperatura, pressão, fluído e vazão. Com este documento é possível identificar minimamente:
– Qual processo de soldagem será utilizado (TIG, Eletrodo Revestido etc);
– Qual tipo de material depositante no processo de soldagem;
– Qual a Instrução de Execução e Inspeção de Soldagem (IEIS);
– Quantas juntas soldadas e qual diâmetro será executada;
– Quantos metros de tubulação serão utilizados;
3.6.1.2 Visita Técnica em Campo (in loco)
Após consultar todos os documentos, o planejador deverá ir à área para certificar-se que tudo que ele reuniu, está de acordo com as instalações. Além disso, é nesta etapa que ele verificará as interferências e recursos necessários para execução. Seguindo imagem abaixo é apresentada uma verificação do equipamento em campo, sendo um Permutador (trocador de calor) do tipo Casco e Tubo.
Considerando que a nota de manutenção para este equipamento é para contaminação de produto, sendo uma possibilidade de furos no feixe (tubos) do permutador, será planejado a abertura do equipamento, inspeção e teste. Sendo assim, o planejador indo a campo, conseguirá identificar as tarefas a serem executadas, bem como sua sequência, quais disciplinas ou especialidades serão utilizadas, quantidade de mão de obra, tempo de execução para cada atividade, interferência, além dos equipamentos e ferramentas necessárias, fazendo anotações em seu controle.
3.6.1.3 Estruturar a Ordem de Manutenção no ERP
Após a ida a campo, o planejador irá estruturar a Ordem de Manutenção (OM) no ERP, inserindo todos os recursos, bem como sua sequência de atividades, além de todos os materiais, conforme as figuras abaixo.
Estrutura das Tarefas na Ordem de Manutenção no ERP
Sequência de amarração de tarefas no ERP
Componentes na Ordem da Manutenção (OM) do ERP
Além disso, o planejador pode elaborar um cronograma de manutenção em um software independente, mas que se comunique ao ERP, como por exemplo o MS Project e/ou Primavera P6. No exemplo abaixo, será possível elaborar uma curva de avanço, verificando se as atividades planejadas estão ocorrendo conforme programado.
Nesta etapa, todas as Ordens de Manutenção (OM) que estiverem planejadas e liberadas para executar, concorrem ao nivelamento de recursos, ou seja, entrar na programação semanal, para serem executadas. Para isso, é necessário criar uma estrutura em forma de matriz, para que as OM’s com criticidade alta, entrem na programação primeiro, garantindo sua execução.
3.7 Programação
Não existe uma fórmula ideal, sendo que cada indústria tem suas particularidades e prioridades, mas sempre pensando na confiabilidade e integridade dos equipamentos. Sugiro que sempre tenham como prioridade a sequência abaixo:
3.7.1 Ordens de Manutenção Oriundas de Planos de Manutenção para Equipamentos de Segurança Operacional
Se no backlog da manutenção tiver alguma nota de falha em algum equipamento de segurança operacional, necessariamente deverá ser priorizada para o nivelamento da programação.
3.7.2 Ordens de Manutenção Oriundas de Planos de Manutenção
Os planos de manutenção são criados pela equipe de Engenharia, para que todos os equipamentos da Unidade Operacional operem de acordo com a sua especificação técnica e projetos. É a busca por garantir a máxima confiabilidade dos equipamentos, evitando falhas e manutenções corretivas.
O plano de manutenção mapeia quaistipos de manutenções são necessários em um determinado período para garantir a saúde e qualidade de um equipamento ou ativo.
Em uma estrutura são colocados quais as tarefas serão realizadas e a periodicidade indicada para cada um (manutenções semanais, quinzenais, trimestrais, semestrais etc.), sendo a resultante destes planos, conforme abaixo:
- Diminuir o índice de falhas dos equipamentos e/ou ativos
- Conserva e prorroga a vida útil dos equipamentos e/ou ativos
- Aumenta a segurança dos processos
- Reduz custos com paradas não programadas de ativos e/ou processos
Para isso a engenharia aplica algumas metodologias para criação e elaboração dos planos de manutenção, sendo:
3.7.3.1 Matriz de Criticidade
Trata-se de umestudo que tem como objetivo estabelecer qual será a estratégia de manutenção utilizada na empresa. Ou seja, qual ativo merece atenção especial naquele momento, de acordo com um tipo de hierarquia. É fundamental deixar claro que a escolha de um ativo não indica que o outro será ignorado.
O objetivo da criticidade é entender quais são os efeitos que a ausência de um equipamento pode gerar naquele momento para o pleno funcionamento dos processos da empresa. Na figura abaixo é possível identificar um modelo de Matriz de Criticidade dos Ativos de uma Planta Industrial.
3.7.3.2 FMEA –Failure Mode and Effect Analysis (Análise dos Modos de Falha e seus Efeitos)
De uma forma simplificada, podemos afirmar que o FMEA é um método para identificar todas as falhas possíveis de um processo, bem como suas formas. Por falhas podemos entender quaisquer erros ou defeitos, reais ou potenciais, que um processo pode apresentar. A prioridade é a identificação de falhas (ou possíveis falhas) que afetam os equipamentos. A “análise de efeitos” refere-se ao estudo das consequências dessas falhas.
O objetivo principal do FMEA é identificar as falhas, priorizá-las em relação ao risco de ocorrerem e suas consequências, e, por fim, tomar medidas para eliminar ou reduzir sua ocorrência. Idealmente, o FMEA atua desde os primeiros estágios conceituais de um projeto. Iniciando sua análise na fase de design e permanecendo durante toda a vida útil do produto ou serviço.
Observação: O FMEA também tem o objetivo dedocumentar o conhecimento atual sobre erros, e as ações realizadas para reduzir os riscos. A razão para isso é gerar um conhecimento importante para amelhoria contínua de processos.
No FMEA é possível calcular o nível de priorização de Risco (NPR) que é um indicador utilizado para classificar os modos de falhas e serve para alertar a empresa quanto à gravidade da falha. Quanto maior for esse indicador, mais urgente é a falha. Então, é necessário agir o quanto antes para impedir que o erro se torne um verdadeiro problema.
Para calcular o Nível de Priorização de Risco, deve-se multiplicar a gravidade (G), a probabilidade de ocorrência (O) e a probabilidade de detectar a falha (D), conforme cálculo abaixo:
NPR = G x O x D
Na gravidade (G), 10 é o mais grave. Na probabilidade de ocorrência (O), 10 é a maior probabilidade, e na probabilidade de detectar a falha (D), 10 é o de menor probabilidade, veja alguns exemplos nas figuras abaixo.
Figura abaixo que ilustra a classificação da gravidade “G”
Figura abaixo que ilustra a classificação da gravidade “O”
Figura abaixo que ilustra a classificação da gravidade “D”
Depois de classificar a gravidade das falhas e calcular o NPR, é hora de elaborar um plano de ação para impedir que as falhas ocorram ou, pelo menos, para diminuir a sua frequência. Nesse plano, você deve especificar em detalhes tudo o que precisa ser feito e quem serão os responsáveis pela execução das tarefas, criando assim o Plano de Manutenção para os Equipamentos, aumentando a confiabilidade e mantendo a integridade dos ativos da empresa, além de deixar os ativos disponíveis.
3.7.4 Ordens de Manutenção Oriundas de Plano de Inspeção
A equipe de Integridade é fundamental na Indústria, sendo ela a responsável por gerenciar e controlar a integridade dos equipamentos, além de garantir o atendimento às legislações vigentes como: Norma Regulamentadora 13 (NR-13) – Caldeiras e Vasos de Pressão e Norma Regulamentadora 10 (NR-10) – Segurança em Instalações e Serviços em Eletricidade.
Os planos de inspeção, garante que os equipamentos operem com segurança, conforme projetados e dimensionados para aquela determinada pressão, temperatura etc. É a garantia que os ativos não irão falhar, ocasionando acidentes a pessoas, meio ambiente e processos.
3.8 Indicadores (KPIs)
Seguindo essa sequência, buscamos a certeza de que serão priorizadas as atividades críticas para a garantia da confiabilidade, integridade e segurança dos ativos, pessoas e processos.
Os indicadores são a forma intrínseca do “P” na sigla PCM, ou seja, o Controle dos processos de manutenção. É aqui que avaliamos, consultamos e através de estratégias, tomamos decisões importantes, baseada em dados, para a busca contínua da segurança de pessoas e processos, através da Confiabilidade, Integridade e Disponibilidade dos Ativos.
Além disso, também é uma forma de medir performance e desempenho do setor de manutenção, assim como produtividade das equipes e processos. Sendo assim, trazendo de forma simples alguns dos mais importantes indicadores do processo de PCM.
3.8.1 MTBF – Mean Time Between Failures
O MTBF ou Tempo Médio Entre Falhas é um dos indicadores mais importantes para o setor de manutenção. Ele é necessário para medir o tempo total de bom funcionamento médio entre as falhas de um equipamento reparável, sendo uma forma de mensurar a confiabilidade do ativo e este cálculo é exemplificado na figura abaixo.
3.8.2 MTTR – Mean Time To Repair
Esse indicador está muito associado à mantenabilidade, ou seja, a facilidade que uma equipe de manutenção encontra em fazer um equipamento voltar a executar suas funções após uma falha. Em outras palavras, o MTTR indica o tempo médio para reparo e calculado conforme abaixo.
3.8.3 Disponibilidade (DISP)
Disponibilidade refere-se à capacidade de um item de estar em condições de executar uma certa função em um dado instante ou durante um intervalo de tempo determinado.
Mesmo com significados semelhantes, para que as diferenças fiquem claras, vamos exemplificar:
A disponibilidade de um equipamento é a porcentagem no qual esse ativo se manteve disponível em um determinado período. Já a confiabilidade será a probabilidade de um equipamento se manter disponível em um período futuro.
Prefere as fórmulas? Confira:
Esses dois indicadores são fundamentais para o Planejamento e Controle da Manutenção, já que o objetivo principal doPCM é garantir e elevar a disponibilidade e confiabilidade dos ativos, otimizando a produtividade da indústria. Por isso resolvemos colocá-los juntos.
Ambos são determinados a partir do MTBF e do MTTR. Mas, antes de calculá-los, vamos entender o significado de cada um segundo a norma NBR 5462, podendo observar nas figuras abaixo.
A figura abaixo ilustra o Cálculo de Disponibilidade
A figura abaixo ilustra o Cálculo de Confiabilidade
3.8.4 Backlog
O backlog pode ser entendido como o tempo de mão de obra necessário para realizar todos os serviços atuais, ou seja, o acúmulo de atividades pendentes. Logo, tal indicador demonstra a relação entre a demanda de serviços e a capacidade de atendê-los.
Podemos entender o backlog como uma carteira de serviço oriunda das atividades de manutenção. Em outras palavras, é a soma da carga horária dos serviços planejados, programados, executados e pendentes do setor de manutenção. Por ser um indicador de tempo, deve ser calculado em minutos, horas, dias, semanas, meses etc., sendo exemplificado na figura abaixo.
Sugiro que todo o backlog deva estar sendo controlado através de um dashboard, onde é possível identificar todas as Ordens de Manutenção, assim como a distribuição e evolução dos gráficos durante os meses, semanas, dias do ano, podendo ser observado:
- Fator de produtividade da equipe de manutenção (aumentou ou diminuiu)
- Carteira de Ordens de Manutenção (aumentou ou diminuiu)
- Capacidade disponível da equipe de manutenção (será necessário aumentar ou diminuir e o porquê)
Na figura abaixo, podemos observar um exemplo desse dashboard, no qual podemos observar o gráfico de comportamento do indicador backlog no ano de 2023.
Infotec Brasil por Felipe Beserra (*)
(*) Felipe Beserra é Engenheiro Mecânico com MBA em Engenharia de Equipamentos e cursando MBA em Gestão de Projetos na Fundação Getúlio Vargas (FGV). Atuei em indústrias do setor de Siderurgia, Oil & Gás, Energia e Mineração, adquirindo experiência em PCM, Confiabilidade e Integridade dos equipamentos.